In questa guida vorrei illustrarvi passo per passo le fasi di progettazione e costruzione di una marmitta per motori a 2 tempi.
Per prima cosa bisogna ricavare la forma geometrica del espansione in base al telaio della moto, se si possiede la marmitta originale o se ne vuole replicare una in possesso basterà suddividerne la forma in vari segmenti di circonferenza e con l'aiuto di uno spago e goniometro calcolare il raggio e l'ampiezza della circonferenza.
In questo esempio ho usato un programma cad in grado di estrarre da una foto gli angoli delle varie curve, a causa della prospettiva della foto si rende necessario l'adozione di una certa precisione nelle misurazioni per compensare l'effetto della foto, effettuando le misurazioni tramite spago e goniometro direttamente sulla marmitta l'errore di misurazione verrà compensato dal assoluta precisione delle curve dato che la misura è reale. Per esperienza personale tutti e due i metodi funzionano perfettamente e i risultati sono apprezzabili in entrambe le tecniche.
In queste foto ho utilizzato la marmitta originale di un Husqvarna 125 per ricavare le dimensioni di ingombro in cui dovrà rimanere la marmitta calcolata.
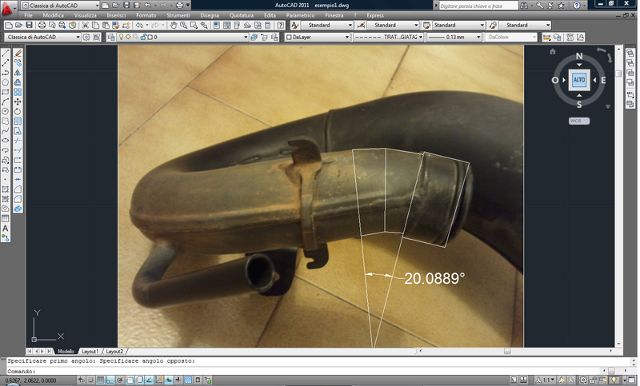
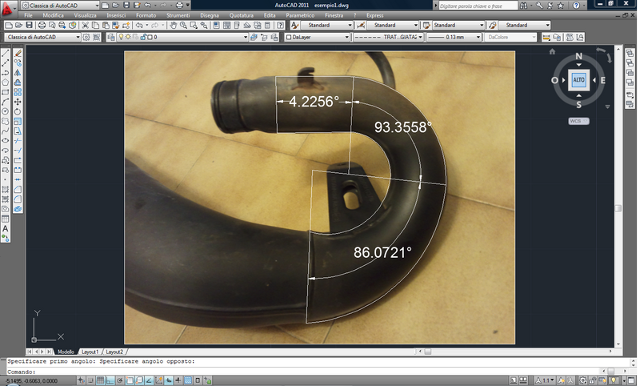
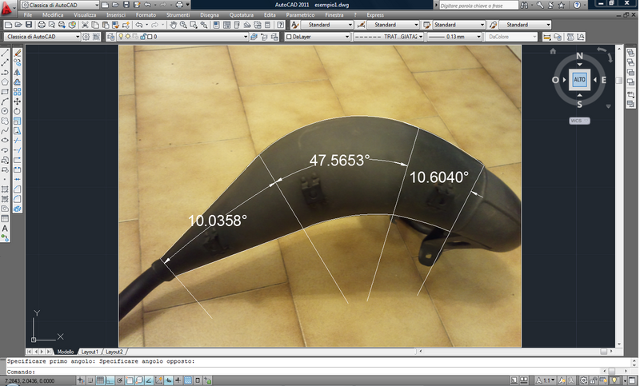
Ottenuto così le misure di base della marmitta si procede ad assegnare il diametro alle rispettive curve, se si vuole replicare una marmitta basterà con un metro da sarta ricavare la circonferenza nei vari tratti e tramite la formula d = crf / π ricavare il diametro
crf sta per circonferenza;
π sta per pi greco
d sta per diametro del cerchio.
Oppure tramite l'elaborazione di una foto messa in scala si possono ricavare i diametri che ci interessano.

Se invece si vuole progettare una marmitta da zero allora tramite programmi come ExhaustCalculator
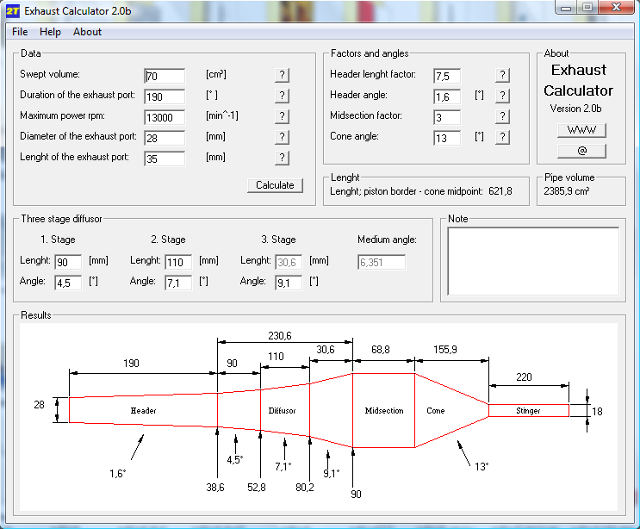
si può ottenere lo sviluppo lineare del espansione per poi applicare i diametri all'espansione.
Questo è un esempio di espansione ottenuta tramite ExhaustCalculator e posso garantire che le dimensioni sono proporzionate al motore per cui è stata progettata e il rendimento ottenuto in prova rispecchiava le aspettative volute durante la progettazione
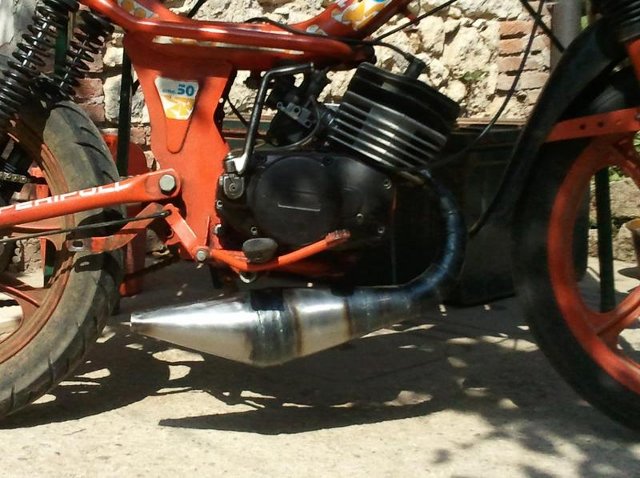
Stabilite le dimensioni e le geometrie delle varie curve di un espansione si procede alla creazione vera e propria dei coni necessari per ottenere le curve desiderate, per fare questo si possono trovare vari programmi sul web, ma il migliore secondo me è Plate'n' Sheet Professional, anche se non è free la versione di prova permette di progettare i semplici tronchi di cono e relativo sviluppo piano.
Trammite plate'n' Sheet accedendo alla schermata iniziale vi è una vasta scelta di figure coniche, in base alle nostre necessità possiamo scegliere quale tipo di figura fa al caso nostro e procedere con l'immissione dei dati richiesti dal programma.
Questa è la schermata iniziale del programma:
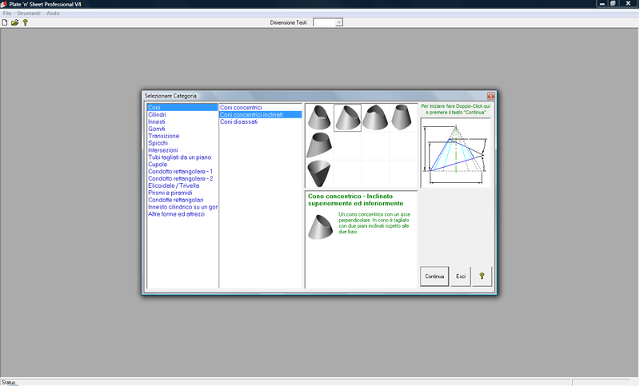
Una volta scelto il nostro tipo di figura il programma ci chiederà di immettere delle misure che sono state precedentemente rilevate tramite spago/goniometro o tramite elaborazione di una foto.
In questo esempio è stata creata una riduzione a 90° composta da 8 coni
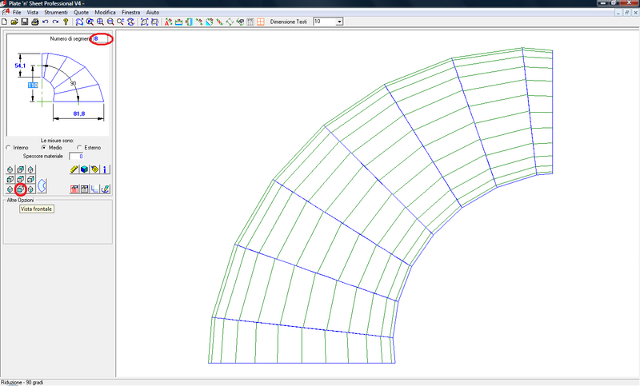
In alto a destra cerchiato in rosso c'è l'immissione del numero di coni di cui verrà composta la curva, un numero troppo basso tenderà a creare una figura spigolosa e poco fluidodinamica per il passaggio dei gas di scarico mentre un numero eccessivo di coni può causare difficoltà nel taglio e nella saldatura di quest'ultimi, per tanto consiglio di visualizzare la vista frontale della curva col tasto segnato in rosso e da qui valutare se il numero di coni è sufficiente o meno.
Quando il numero di coni e i dati inseriti per formare la curva ci soddisfano basta esportare in tutto in AutoCAD, dato che lo sviluppo dei coni difficilmente rientra in un foglio di formato A4 è consigliabile esportare tutto in un file dwg e in seguito impaginarlo e portarlo a stampare con plotter in una qualsiasi copisteria.
Qui sotto viene mostrato come esportare lo sviluppo piano dei coni della curva, come prima cosa bisogna visualizzare lo sviluppo tramite il pulsante cerchiato in rosso.
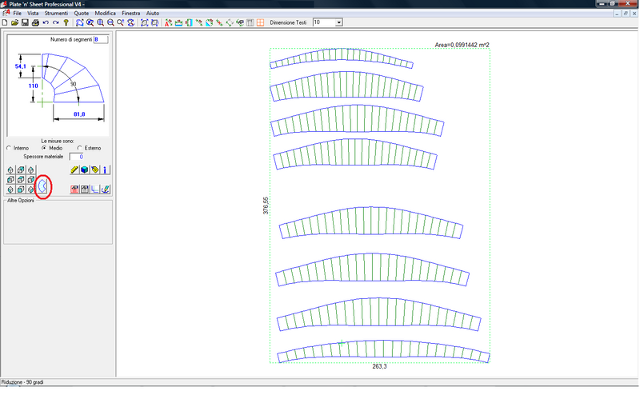
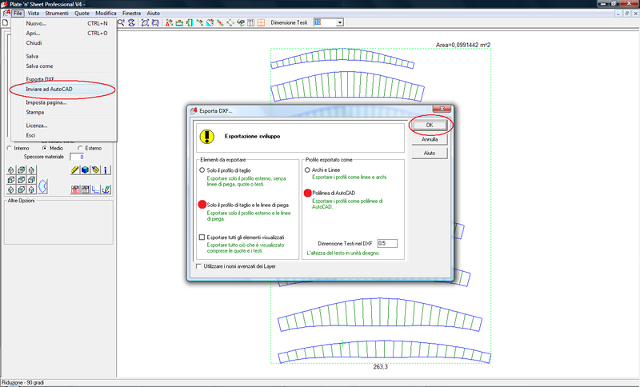
A questo punto basterà cliccare su File inviare a AutoCAD
si aprirà una schermata Esporta DXF, accertarsi che le selezioni siano come in foto e cliccare ok
aprire AutoCAD e create un nuovo file, a questo punto Plate'n' Sheet chiederà di selezionare il punto di inserimento nella finestra di AutoCAD diamo ok quindi andando sulla schermata di AutoCAD clicchiamo su un punto qualsiasi dello schermo, poi con un secondo clic del mouse andremo a definire gli assi x e y del disegno, a questo punto Plate'n' Sheet genererà gli sviluppi dei coni sulla schermata.
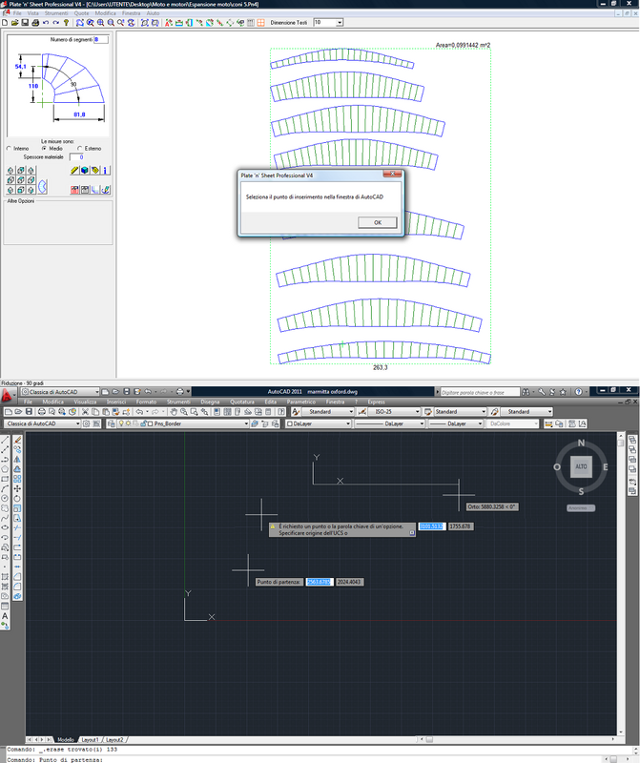
In alternativa si può esportare direttamente su un unico file dxf (cliccare su File Esporta DXF) e farlo tagliare al laser ma in questo modo lo spazio di taglio non verrà minimizzato e i costi del materiale aumenteranno di conseguenza. Il mio consiglio è di portare tutto in AutoCad e poi disporre i vari coni e impaginare il tutto.
Sconsiglio di far tagliare subito su lamiera i coni appena ottenuti se non si è certi che le dimensioni impostate consentano di creare una marmitta perfetta per il telaio della moto; per tanto la scelta migliore è quella di realizzare un prototipo in cartoncino e realizzare così una marmitta prototipo da provare sulla moto.
Questo è un esempio di marmitta per Husqvarna 125
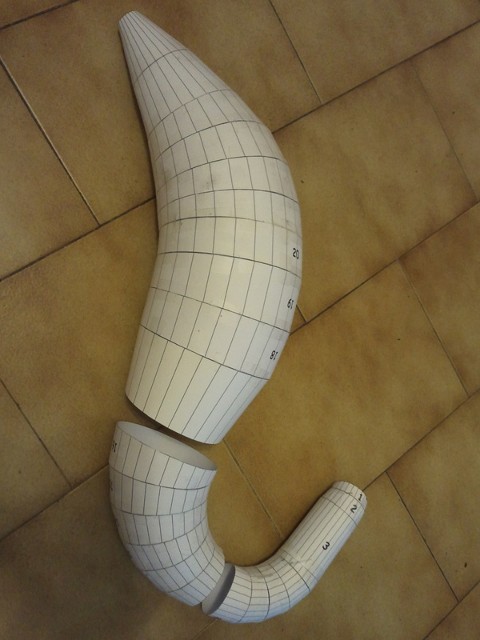
Una volta stampati i nostri coni su carta si procede ritagliandoli e unendoli in modo da creare una marmitta di carta per una verifica finale direttamente sulla moto.
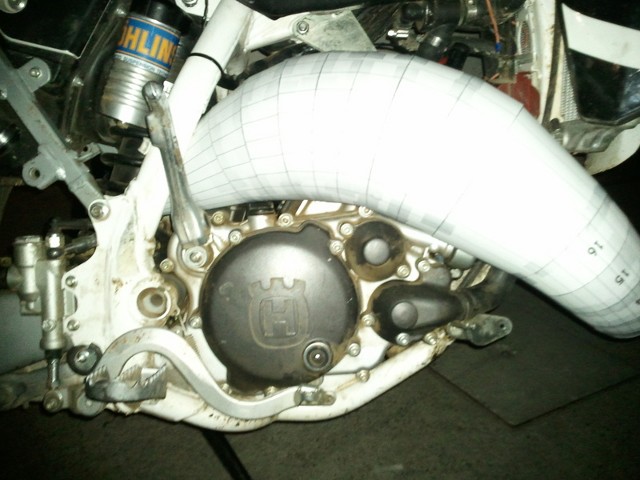
Se tutto è stato ben dimensionato e progettato si può procedere con il taglio della lamiera. Il materiale ideale sarebbe lamiera di acciaio da 0.8 -1mm se saldato a cannello mentre 1,0-1,2mm se saldato a tig volendo si può usare anche lamiera di titanio da 1mm ma il costo è doppio rispetto al acciaio.
Per il taglio dei coni il top è il laser o il plasma dato che Plate'n' Sheet permette di ottenere il disegno in dxf; ma bisogna fare attenzione alla precisione del macchinario perché il taglio deve avvenire con la precisione del decimo di millimetro 0.1mm altrimenti un errore maggiore nel taglio porterà alla fine quando si dovrà far combaciare i vari coni ad una differenza di 1-2 mm con relativi problemi di saldatura.
Se non si ha la possibilità di far tagliare al laser i coni allora si può stampare su carta il profilo di taglio e incollarlo sulla lamiera per poi tagliare con le forbici da lamiera; ovviamente più è spesso il materiale e più sarà difficile il taglio. Una volta tagliati tutti i coni si può procedere con la fase di calandratura, se possedete già una calandra questa procedura vi sarà molto semplice, in alternativa potete comprarne una o adirittura costruirla dato l'estrema semplicità del macchinario.
Calandra Home made di facile realizzazione e dal ottimo funzionamento
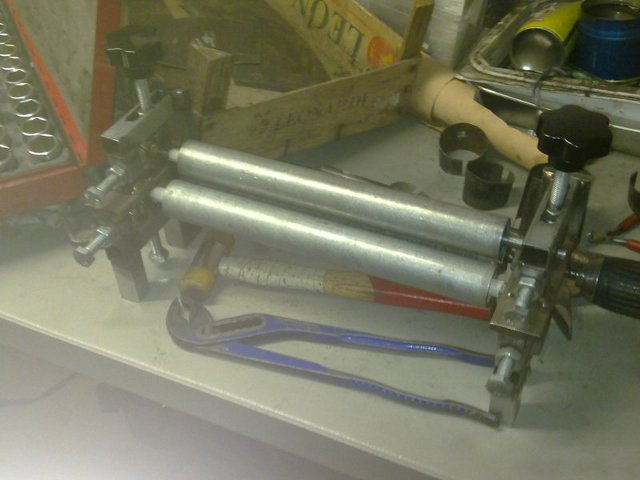
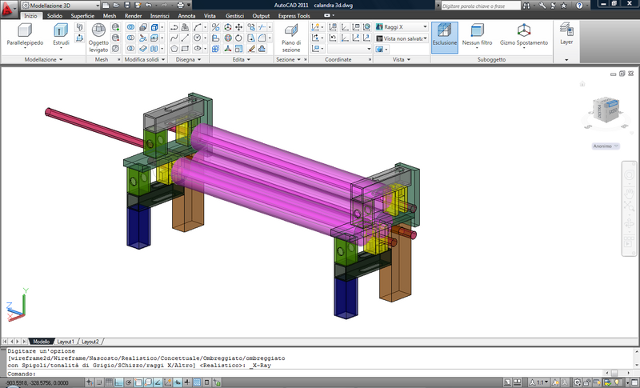
Una volta calandrati i coni possiamo unirli con del nastro isolante per verificare che combacino tra di loro, in caso contrario con della carta vetrata levigare i bordi per renderli perfetti
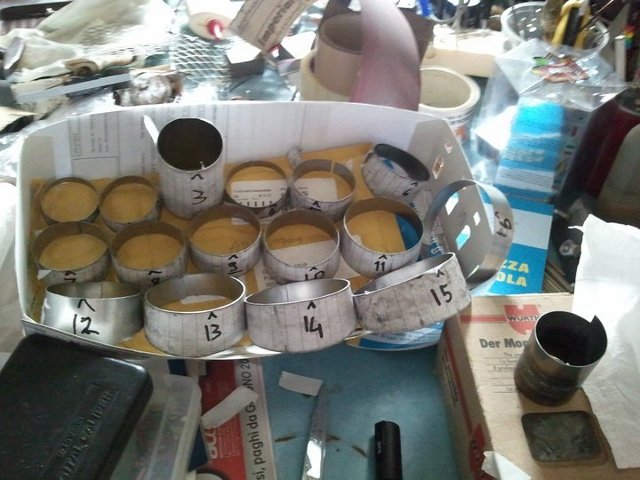
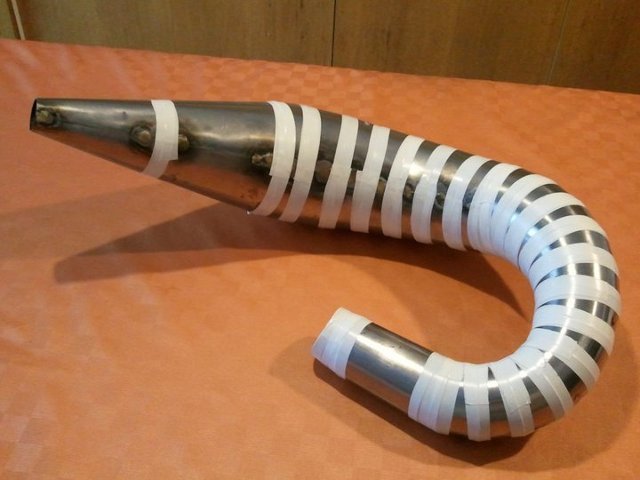
a questo punto non rimane che saldare i nostri coni a cannello o a tig
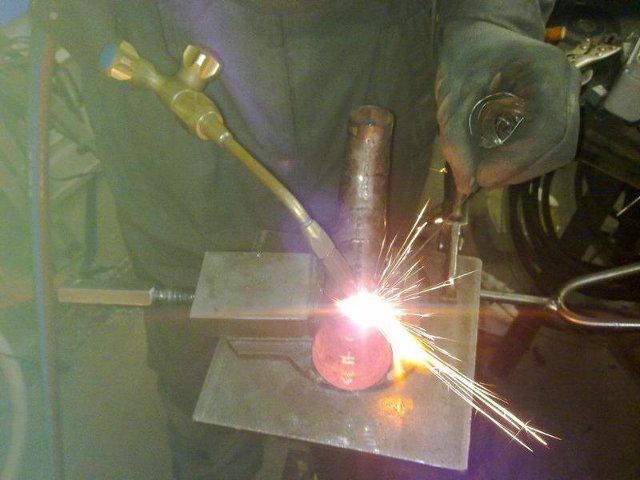
consiglio di procedere saldando tratti di curva per verificare sempre in tempo reale sulla moto il corretto allineamento, questo è necessario perché la lamiera si deforma col calore delle saldature e potrebbe essere necessario apportare delle modifiche in opera
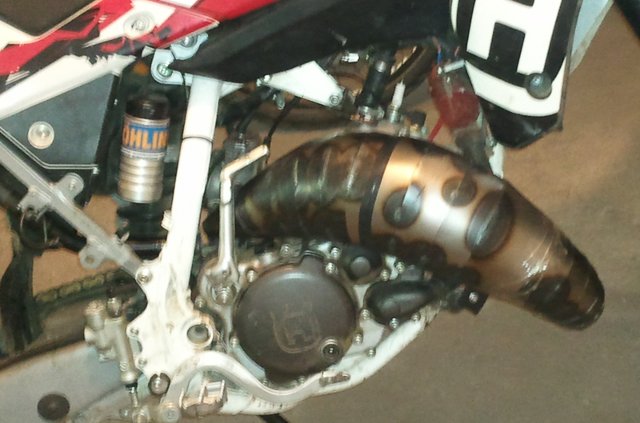
Terminata la saldatura di tutti i coni non resta che saldare uno spillo, una staffa e un attacco al cilindro, consiglio la brasatura ad ottone così da ottenere una saldatura robusta e indistruttibile dalle vibrazioni.
Con questo si conclude la guida sulla creazione di una marmitta per motori 2t, spero di aver donato un contributo a tutta la comunità con la mia esperienza in materia.
Ciao da Crimas